The production of PVC pipes involves a series of intricate processes that transform raw materials into essential components for plumbing, construction, and various industrial applications. Understanding these key processes can provide insights into the quality and efficiency of the final products. Let’s explore the main steps involved in a PVC pipe factory.
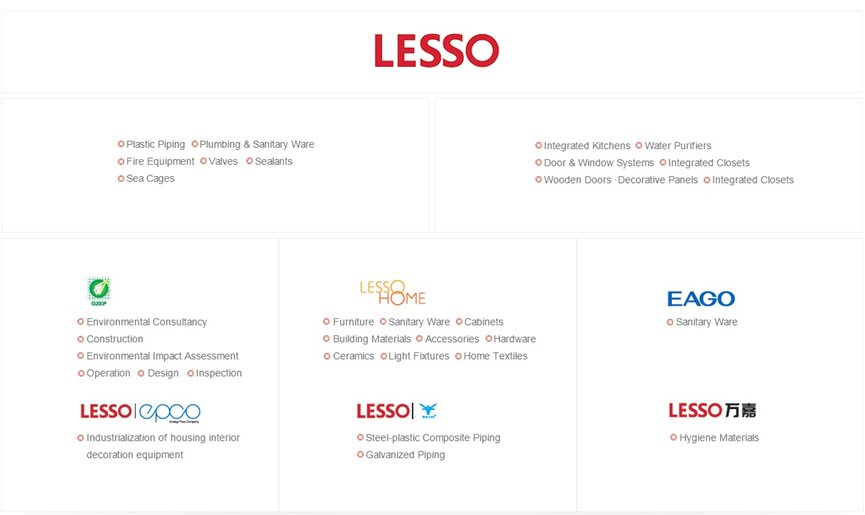
1. Raw Material Preparation
The first step in the PVC pipe manufacturing process is the preparation of raw materials. PVC resin, along with various additives, is sourced and stored in a controlled environment. These additives may include stabilizers, lubricants, and colorants, which enhance the properties of the final product. Precise measurements are crucial at this stage to ensure that the PVC mixture meets the desired specifications.
2. Mixing
Once the raw materials are prepared, they are fed into a mixer where they are combined thoroughly. This mixing process ensures that the additives are evenly distributed throughout the PVC resin. The result is a homogeneous material that is ready for the extrusion process. The quality of this mixture plays a significant role in determining the strength, flexibility, and durability of the finished pipes.
3. Extrusion
The extrusion process is where the magic happens. The mixed PVC material is fed into an extruder, where it is heated and melted. As it exits the extruder, the molten PVC is shaped into a continuous pipe form through a die. This section is critical, as the temperature and pressure must be carefully controlled to ensure consistent wall thickness and quality.
4. Cooling
After extrusion, the newly formed PVC pipe is cooled to solidify it. This is typically done using a water bath or air cooling system. Proper cooling is essential to prevent warping and ensure that the pipe retains its shape and structural integrity. The cooling process also affects the final properties of the pipe, including its strength and impact resistance.
5. Cutting
Once cooled, the long lengths of PVC pipe are cut into specified sizes. This is usually done using automated cutting machines that ensure precision and consistency. Accurate cutting is vital for meeting customer specifications and ensuring that the pipes fit seamlessly into plumbing and construction applications.
6. Quality Control
Quality control is a crucial step in the production of PVC pipes. Samples are taken from each batch to undergo rigorous testing, including pressure tests, impact resistance tests, and dimensional checks. This ensures that the pipes meet industry standards and customer requirements for performance and safety.
7. Packaging and Shipping
After passing quality control, the PVC pipes are packaged for shipment. This step includes labeling, bundling, and preparing the pipes for transportation to distributors and customers. Effective packaging protects the pipes during transit and ensures they arrive in excellent condition.
Conclusion
The production of PVC pipes in a factory involves several key processes, from raw material preparation to packaging. Each step is critical to ensuring the quality, durability, and performance of the final product.
LESSO stands out in the PVC pipe manufacturing industry, employing advanced technology and strict quality control measures throughout these processes. With a commitment to innovation and excellence, LESSO ensures that its PVC pipes meet the highest standards, making them a trusted choice for customers worldwide. By choosing LESSO, you can be confident in the quality and reliability of your PVC piping solutions.